Fitrun Bearing would like to share with you the basic knowledge of ball bearing manufacturing, mainly on the manufacturing process. We split the contents into 7 blocks as below.
1. The Process
The ball bearings comprise 3 components; bearing rings, rollers, and cages. Each of these components goes through a unique process itself. Let’s look at these processes
1.1 The bearing rings (it’s inside and outside)
Raw material – forging – turning – treatment through heat – grinding – assembling
1.2 Rollers
Raw material – turning – treatment through heat – grinding – assembling
1.3 Cages (made of brass or stainless steel)
Raw material – casting – turning – milling – deburring – assembling
2. The Material Used in Bearing
This refers to the kind of material used in bearing rings, rollers, and cages. We have more available information on bearing made from steel which can be accessed by checking the bearing steel composition and different standards for model interchange of.
2.1 Bearing Ring & Roller
The usual material used is high-carbon chromium-bearing steel: Gcr15 (52100), Gcr15SiMn (1.3520). there are however other materials used that include: carburized bearing steel, abrasion and corrosive resistance bearing steel, heat resistance bearing steel.
The material used for the bearing ring and roller should have the following requirements:
- The surface of the load capacity should be high
- The abrasion resistance should be commendable
- Elastic limit should be high
- The material should have hardness qualities
- Tough material
- It should be stable enough
- Material that does not rust
- High processing performance
2.2 Bearing Cage
The bearing cage is made from the following materials with their specific requirements:
a) Non-ferrous metal – Brass HPb59-1, bronze QAL10-3-1.5, Aluminum alloy LY11CZ
b) Ferrous Metal – Quality carbon steel thin plate
c) Non-metal – Engineering nylon, phenolic adhesive
3. Forging
During the process of forging, the bearing ring is made, and it is also known as blank processing.
3.1 There are reasons why the bearing ring needs to be forged. Those reasons include:
- To get the semi-complete ring that looks like the bearing so that the efficiency of the metal material is increased.
- To reduce the mechanical work that is carried out using machines
- To reduce the production cost.
- To get rid of any defects that the metal may have
- To enhance the organization system of the metal so that the metal has better-streamlined distribution and is more contact
- To increase the bearings’ life span so that they can last longer.
3.2 Forging can be done in 3 different ways:
a) Hot forging
This involves the heating of metal which is done above the crystallization temperature and is a method that is often used.
b) Cold forging
This method requires that the metal be forged using room temperature and is a method that is barely used.
c) Warm forging
It is a method that involves forging metal using temperatures that are in between hot forging and cold forging. This method has still been developed and tested.
3.3 Bearing Ring Forging Process
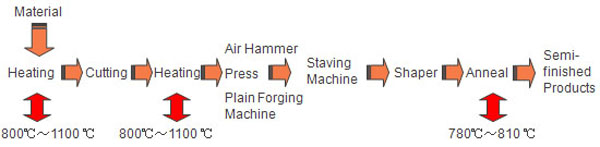
4. Turning
The turning process is only done for and to the semi-complete bearing rings and rollers. This process is also known as the forming process.
4.1 Turning is done for the following reasons:
- To ensure that the bearing ring and roller are of the same shape as that of the complete products.
- To endure that the bearing and roller are fit enough to go through the grinding process.
4.2 The turning process is done using two methods:
a) Integrated Processing
This helps complete the turning process in a single machine which is appropriate when the production size is intended to be small.
b) Distributed Processing
It is done to make sure that one turning procedure is completed in one machine which is more appropriate when the production size is intended to be large.
4.3 Bearing Ring Turning Process

4.4 Roller Turning Process

Oftentimes, the equipment and machinery that are used is specifically for the bearing process and they are placed according to the distributed procedure that they are supposed to follow.
5. Heat Treatment
This is the main and most important procedure that helps increase the inner quality of the bearing.
5.1 Heat treatment is done for various reasons, including:
- To enhance the bearing’s mechanical functioning by changing the material structure through treatment.
- To improve the bearing’s inner quality to increase its lifespan. Heat treatment ensures that it is tough, is abrasive resistant, among others.
5.2 Bearing ring and roller heat treatment process

6. Grinding
This is the final process for manufacturing the bearing and roller. It is also known as finished product processing.
6.1 The reason grinding is done is because:
- To ensure that the bearing ring and roller are of the required sizes and shapes
- To prepare the rings and rollers that meet the specifications for the bearing assembly.
Normally, it’s processed by distributed procedure; or the machines can be connected to integrate into a production line by material loading and unloading equipment to enhance the production efficiency.
The grinding process is usually done using the distributed procedure or the connection of machines is done so that it integrates into a production line. This is done by loading material or unloading the equipment so that the product’s efficiency is increased.
6.2 Bearing Ring Grinding Process

6.3 Roller Grinding Process

7. Bearing Assembly
The final process is the bearing assembly. It is very crucial and determines the effectiveness of the performance of the bearing.
7.1 The main purpose of this process is:
- To put together the completed components including: out rings, inner rings, rollers, and cages, and make them into finished bearings.
- To assemble the finished components placing them according to their different precisions, clearances, and special requirements of bearings depending on their different technological requirements.
7.2 Bearing Assembly Process
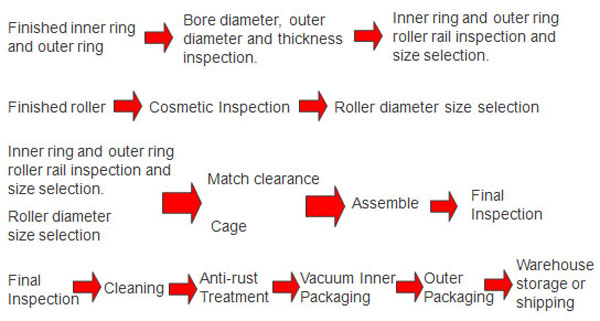
This article has provided insight into the basic knowledge that you need to have on how bearing manufacturing is done. We hope it has been helpful enough and we recommend that you watch ball bearing manufacturing process video (open in new tab) on our YouTube channel for more information on this. As a ball bearing manufacturer, we continue to work hard to ensure that we give our customers the best high quality bearing products.